|







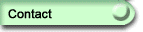
|
Where does the essence of уюдн-technology lie?
For simplicity the workings of уюдн-technology can be broken down to the
following stages:
Superfinish operation and final grinding of
уюдн particles by the microrelief projections
|
Clearing up of the microrelief of the contact spots of the mating
parts
|
|
|
As is evidenced by practice, the special form of
уюдн microparticles (microscales) and appropriate additions to
уюдн compound are capable to better clear up the microrelief,
than available detergents.
In the course of the microrelief clearing a large quantity of previously
packed and lapped contaminants are being dumped
into the oil (products of decomposition and deterioration of lubricants).
Too large quantity of these can greatly affect
the efficiency of the tight hard-working. The oil need be
changed in this case.
уюдн microparticles are apt to clear up the microrelief
practically from all contaminants (additives, friction modifiers,
metal conditioners). If the cleaning proceeds normally,
in no more than 1 h of the running-in of уюдн compound one can observe
changes in the mechanism performance.
Top
|
Hard working of уюдн particles by tight packing
into recesses of the microrelief of the contacting surfaces of the parts
|
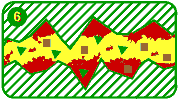
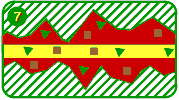
- standard lube
- particles of contaminants
- metal particles
- уюдн particles
|
|
The above described operations of their own result in
more efficient wear protection, than any standard
lubricants and additives can ensure. The heat release at the surface
is dramatically reduced and the oil wedge, though contaminated, is more effective.
Due to compact work-hardening there is ensured a tight contact
of уюдн microparticles and the corresponding additions thereto with the metal of
the near-surface layer of the contact spot. In the presence of catalysts
and due to the energy produced, there is initiated formation
of new crystals with more spatial crystal lattice (Fig.6).
The resulting bulk of the crystals start to "lift" over
the surface of the contact spot and make up for the wear. The remaining
уюдн particles accumulate on the surface of the forming layer and
level it off. The thickness of the layers is proportional to the quantity of
the particles, work-hardened into the relief microrecesses, and to the energy,
released due to friction and contact, i.e. is a function of wear (Fig.7).
The layer thickness is regulated automatically. As long as the friction and contact
energy exists, the layer keeps growing. The growth results in
compensation of clearances, reduction of the energy release on
the surface. All this leads to termination of the substitution reaction
and inhibits further growth.
Top
|
[Technology]
[Products]
[Consultations]
[Links]
[News]
[Site map]
[Contact]
© WM-e-Shop.com, 2000 - 2005 "XADO-technology"
|