|







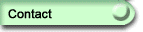
|
General
What is XADO-technology ?
XADO-technology is a technique of reconditioning of machines,
assemblies and mechanisms, which were not mechanically injured
in the standard mode of operation (without disassembly and interference with
functioning). XADO compounds are fully analogous
and synonymous to the trademark PBC-technology.
What is XADO reconditioning compound?
XADO reconditioning compound is a multicomponent fine
mixture of natural minerals, additions and catalysts.
The main feature of the compound is that
it is able to form with the surface layer of
metal at friction and contact spots a cermet
protective coating as a result of the reaction of substitution of metal ions
in crystal lattice nodes. The substitution reaction results in formation
of new crystals with a more spatial crystal
lattice, which raise over the surface of the
contact spot to make up for the wear. Besides:
- XADO is a compound, which can easily dissolve in oils,
including synthetic ones, and other carriers.
The amount of the compound required for treatment will not change the oil viscosity.
Oils are viewed as the compound carriers and a heat exchange medium.
The grade and quality of such oils are of no importance.
- XADO is not a abrasive-like material.
Never and under no conditions XADO can become the major cause
of the mechanism destruction, even in case of a
multiple overdosage.
- XADO "operates" only where friction exists, i.e.
where exists the energy, required for the substitution reation to proceed
What properties does the protective cermet coating possess?
Basic properties of the cermet protective coating:
- Microhardness of surfaces 400-450 kg/mm2
- Friction coefficient: 0.003-0.007;
- Compressive stresses: 250 kg/mm2;
- Eliminates by 100% the "metal-to-metal" contact,
replacing it with a "cermet-to-cermet" contact;
- Is not incompatible with the steels, where it forms, as between it
and surface layers of the parts there is no distinct interface. Holds onto the steel
surface better, than chromium, nickel and variuos facings;
- Completely corrects hydrogen cracking of rubbing surfaces of the parts;
- High corrosion resistance.
- Will not spall on deformation and shocks
- Can be renewed as it deteriorates with time by a repeated XADO-treatment
What causes wear and corrosion of machine parts?
The overwhelming majority of machine and mechanism parts are manufactured out of
a small number(15-20 names) of iron alloys (steels and cast irons).
The main factors, which make these wear and corrode, are:
- Electrochemical corrosion (chemical instability)
Steels and cast irons can be called solid solutions of chemically
instable elements. The electrochemical corrosion is
the most destructive factor for friction and contact surfaces.
In all mechanisms all parts are made of materials,
including metals, with different chemical composition. In service
the parts are rubbing with different relative dicplacements.
As a result, in friction and contact zones due to inhomogeneity
of the metal structure in the presence of an excellent electrolyte
(oil) there emerge electromagnetic fields in microvolumes, which create
perfect conditions for electrochemical corrosion procedure.
- Hydrogen embrittlement (cracking)
This factor is intrinsic to the nature of metals and methods of production thereof.
The existing remedies are highly expensive.
- Inability to "dry" friction
Practically all existing today constructions are provided
with lubrication systems and sealing arrangements.
Eventually not a single sealing design proves capable of containing
lubrication within crankcases at "gland-shaft" contact due to
electrochemical corrosion. All this leads to low wear resistance
and inability of the existing to date constructions to "dry" friction
(friction without oil), which makes steels and cast irons readily fuse
over the surface due to microwelding between the microrelief projections.
- Loss of structural strength and surface annealing with
relatively low heating
- Great weigth of parts, articles
What does XADO-technology treatment mean?
The XADO-technology treatment includes a number of process operations,
targeted at attainment on friction and contact surfaces
of machine parts of a cermet
protective coating of a thickness sufficient to compensate the wear
by utilization of XADO reconditioning compound.
The positive results of such treatment are obtained, if
on the rubbing surfaces of any mechanism there will be delivered
and worked on a required quantity of said reconditioning compound
over the required time.
What machines and mechanisms can be reconditioned through XADO-technology?
All types of machines and mechanisms can be treated using XADO-technology,
provided 2 conditions are met:
- If at least one part is made of metal;
- If the parts and mechanisms have no past-repair wear and mechanical damage.
In terms of XADO-technology any mechanism of any design must be viewed
simply asa set of parts:gear wheels, bearings, sliding friction
surfaces. Loadings and rotational speeds of such mechanisms, steel and cast iron grades,
oil used have no importance.
The mechanism design is considered from the point of view of
delivery of the reconditioning compound
to this or that rubbing pair only.
How can XADO be delivered to the rubbing surface of machine's parts?
To deliver XADO to the rubbing surface of machine's parts use
can be made of the oil, employed in this particular unit.
This carrier ensures removal from the rubbing and contacting
surface of oil (additives) deterioration and decomposition products
in the process of the working-on and cleaning of XADO.
Practical applications have refined 4 main XADO delivery routes:
- Using standard lube system.
This applies to: crankcases of internal combustion engines, compressors,
hydraulic system tanks, machine tools' lube reservoirs.
- Partial disassembly and application of the compound to the rubbing pairs.
This applies to: central cylinder set of internal combustion engines, compressors, reducers
of tobacco machines, pump bearings.
- Application directly to open assemblies and mechanisms.
This applies to: chain transmissions, open gear wheel transmisions, machine tools'
slides, rails, parts, which are worked on metalworking machine
tools, for example, during working of rolling bearings and rolls.
- Application via fuel from tank. This is, for example,
XADO application to HPFP diesel engines.
How to work with XADO compound most comfortably?
XADO is on offer in the form of a gel-like suspension and
greases.
- XADO Gels readily dissolve within 10-15 s in any petrochemical
(both mineral and synthetic). Should you have any difficulties with XADO application
in any particular case by squeezing it out of its tube due to a specific design
of the mechanism, we recommend the following technique. Dissolve the required amount of
XADO in any petrochemical in proportion 1:2. Use a syringe with
a tubing length attached thereto to introduce the resulting mixture.
- XADO Greases. The volume and application procedure for XADO-greaseas
depends on the design of a particular assembly and is described in service
instructions for those assemblies and mechanisms.
What is meant by "standard mode of operation" ?
By the "standard mode of operation" we mean following the operational
conditions, specified in the instructions. For example, coolant temperature must not
exceed 100o Ñ.
Who holds the copyrights over XADO-technology?
The copyright over XADO-technology are held by a group of individuals.
"XADO" Corporation, which acts on their behalf, is authorized to grant
international licenses for using XADO-technology and for exclusive distribution.
[Technology]
[Products]
[Consultations]
[Links]
[News]
[Site map]
[Contact]
© WM-e-Shop.com, 2000 - 2005 "XADO-technology"
|